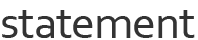
Bio
Brian was raised in northern Utah where he spent much of his time adventuring in Utah's Rocky Mountains and red sand deserts. He received a BFA from Utah State University and his MFA from the New York State School of Ceramics at Alfred University. He has been a resident artist and worked for several art centers and Universities including The Mendocino Art Center, Watershed Center for the Ceramic Art, Arrowmont School of Arts and Crafts, the Art Institute of Chicago and Maryland Institute College of Art. Currently located in Eastham Massachusetts, Brian is the Ceramics Studio Manager at Truro Center for the Arts at Castle Hill and he makes work in his home studio.
Artist Statement
My work is a snapshot of what I find curious in material culture: the complexity of our desire for both the manufactured and the handmade to exist in the same place. By combining representations of form, color and the symbolic residue of various making processes, I hope to tease out a conversation about how we value the objects we keep around us. I do not intend to formulate a rubric for judgment, but rather to draw from signifiers in my environment in order to coerce a play between the processes of making and expectations.
Technical Statement
My studio practice revolves around a variety of making processes. Slip casting, press molding, wheel throwing and hand-building are used and often combined in each piece. I use a white slip casting body that also accepts hand-built attachments from the same but slightly altered recipe and a red clay body that is usually covered with white slip.
Although I do use the pottery wheel, simple and quickly made plaster molds are used for much of my work. The majority are 2-part molds made by cutting a 1-part mold in half with a saw. Purposefully overlooking many time consuming strategies designed to eliminate the evidence of process.
My glazes consist of two bases: a "plastic" matte and a transparent gloss that are fired to cone three (approx. 2100F). These glazes were formulated to simulate traditional glossy pottery glazes and also attempt to mimic colored plastic or tool-dip.
Although I do use the pottery wheel, simple and quickly made plaster molds are used for much of my work. The majority are 2-part molds made by cutting a 1-part mold in half with a saw. Purposefully overlooking many time consuming strategies designed to eliminate the evidence of process.
My glazes consist of two bases: a "plastic" matte and a transparent gloss that are fired to cone three (approx. 2100F). These glazes were formulated to simulate traditional glossy pottery glazes and also attempt to mimic colored plastic or tool-dip.